Richard refurbs the desktop CNC!
Richard got the desktop CNC working! He put a new control board in the MaxNC and now it creates sawdust in compelling ways!
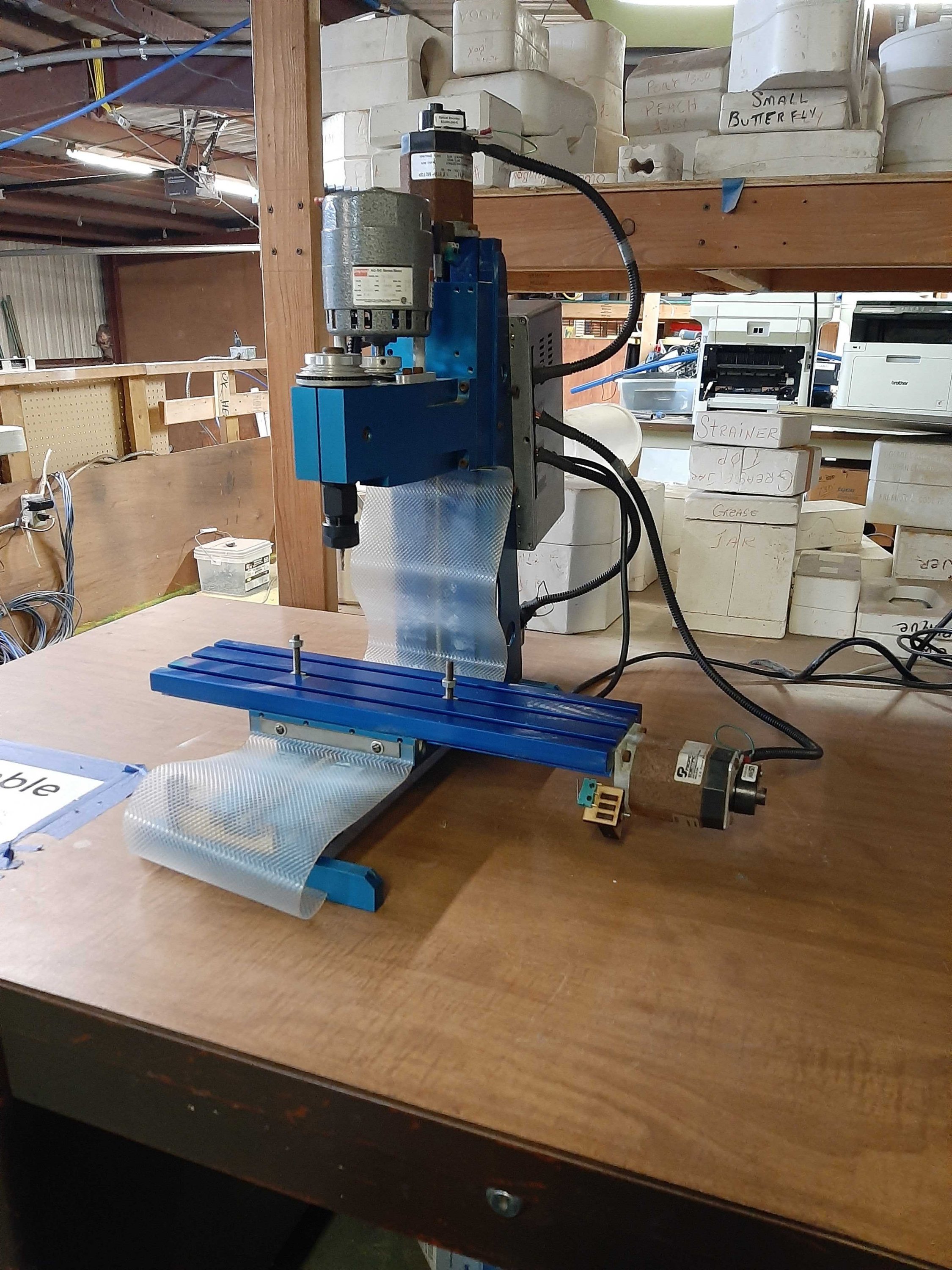
Makers create reactive LED display at the DayLIT event.
ctag reinforces a table during clean-up day.
Members and non-members alike gather to make paper flowers for Wedding Week.
Richard got the desktop CNC working! He put a new control board in the MaxNC and now it creates sawdust in compelling ways!
We drink an obscene amount of Mountain Dew here. With the new crusher we’re going to recoup some cash recycling the cans 😉
Come one come all to the next Nerd Rummage Sale!
Who:Â You!
What:Â A rummage sale where people hock their nerd\geek\fandom leftovers.
When:Â Oct 1st, 9AM to 3PM
Where:Â 414 Stevens Ave
Vendor Sign Up:  https://forms.gle/zQ71cF77atHDTkcS8
Copyright © 2024 Makers Local 256 | Powered by Simple Helix and WordPress